Robots that can climb poles are under development and are expected to be used in the inside/outside maintenance of buildings, observations of disaster scenes from a height, pruning trees, and more. Climbing robots are useful when a task requires the use of far-reaching tools or is risky if carried out by humans. These robots can be equipped with video cameras, microphones, other sensors, and robotic manipulators to perform certain tasks. Here in this project a new type of pole-climbing Robot mechanism is proposed, the configuration and characteristics of the mechanism are introduced. The Robot mechanism action of hold pole, put pole, main move, and process of climbing pole, fixed to the pole, and across barriers are analyzed.
The principal theory which is used in the pole-climbing Robot is elaborated the control system of pole-climbing robot is designed. Analysis shows that: The mechanism has the characteristics of compact body, easy control, good move characteristics, and is a promising application of pole-climbing Robot structure. Our prototype of ‘Pole Climbing Robot’ has the capability to climb over the poles and perform the desired task smoothly.
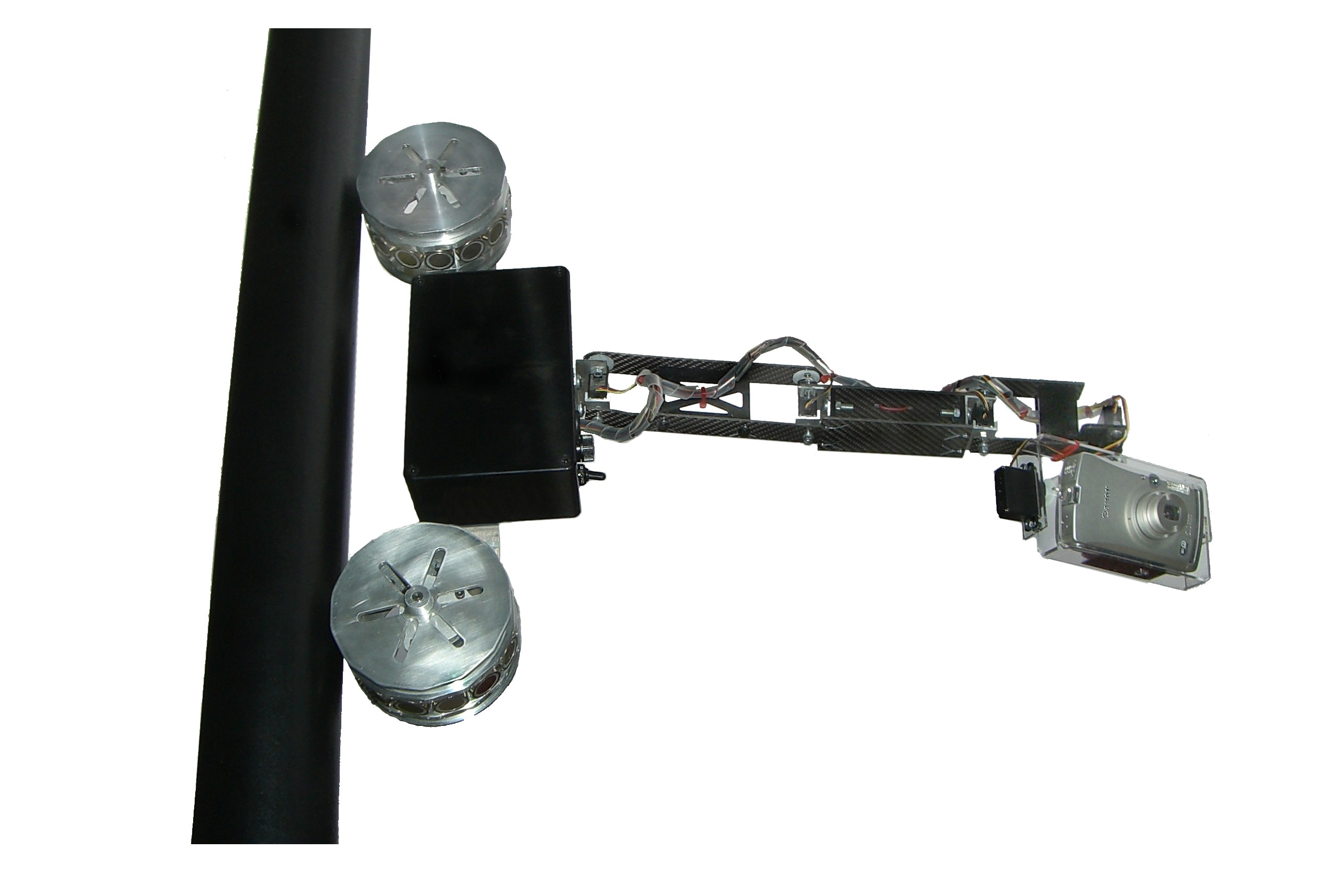
In this project we are using a new gripping mechanism for climbing the pole for that we are using two power supplies one from lead acid battery and another from directly ac power .The H Bridge is used to control the direction of the motors used for climbing purpose. Two switching arrays are used for controlling the robot The RF modules used here are STT-433 MHz Transmitter, STR-433 MHz Receiver, HT12E RF Encoder and HT12D RF Decoder. The two switches are interfaced to the RF transmitter through RF Encoder. The encoder continuously reads the status of the switches, passes the data to the RF transmitter and the transmitter transmits the data. This project uses regulated 5V, 9V 500mA power supply. 7805 three terminal voltage regulator is used for voltage regulation. Bridge type full wave rectifier is used to rectify the ac out put of secondary of 230/18V step down transformer.
As an alternative, we developed and analyzed a climbing method . The climbing mechanism is equipped with a servomotor and a warm-wheel reduction mechanism which has non-back-drivability. It can stay on a tree using its own weight, since the center of its mass is located outside of the tree. A climbing robot that uses its own weight, with one active wheel and two passive wheels,was described in 2010 [3, 4]. However, the climbing speed of the robot is low,since the robot can slip off when an active wheel slips. These robots can only climb straight up; they cannot climb in a spiral. Therefore, it is difficult to observe omnidirectionally and, for example, to prune trees after climbing up.
Applications of climbing robots will be expanded if they can climb not only straight up but also spirally. Most trees are conical thicker at the bottom and gradually becoming thinner with increasing height. This is called the stem taper in the logging/timber industry. When a climbing robot using its own weight climbs straight up a conical pole, the pole can get stuck in between the robot’s wheels because the robot tilts downward as it climbs the conical pole. Moreover, it can be difficult to control the steering angle of the active wheels during the climb, even if the robot has not gotten stuck in the tree.
This paper proposes a postural adjustment mechanism to be used with a climbing robot that has four wheels. It consists of two 1-degree of freedom (DOF) two-link arm mechanisms, one located on the top side and the other underneath, to make the robot lightweight.
Working
The RF modules used here are STT-433 MHz Transmitter, STR-433 MHz Receiver, HT12E RF Encoder and HT12D RF Decoder. The two switches are interfaced to the RF transmitter through RF Encoder. The encoder continuously reads the status of the switches, passes the data to the RF transmitter and the transmitter transmits the data.
This project uses regulated 5V, 9V 500mA power supply. 7805 three terminal voltage regulator is used for voltage regulation. Bridge type full wave rectifier is used to rectify the ac out put of secondary of 230/18V step down transformer The data is received by the RF receiver from the antennapin and this data is available on the data pins. Two Data pins are provided in the receiver module. Thus, this data can be used for further applications.
Mechanism of climbing robot using its own weight
It is desirable that a climbing robot has more than two wheels, since it is quite possible for a wheel to slip out of place; more wheels will contribute to stable climbing. As shown in Figure 1, our climbing robot is equipped with four active wheels. Two wheels are located on top (numbers 1 and 2) and two wheels are located on the bottom (numbers 3 and 4). Each wheel is placed at the same angle ± π / 4 rad relative to the x-axis when viewed from the top of the cylinder.
The active wheel is driven by a DC servomotor via a warm-wheel reduction mechanism. The warm-wheel reduction mechanism, which has non-back drivability, allows the robot to be at rest without any energy expenditure when the input electric current for the servomotor is zero.
We ensured that the center of mass of the robot is located outside of the cylinder by placing the control system at the side of the down-side active wheels. Each of the four active wheels has a steering system to control the steering angle. The steering system is driven by a DC servomotor via a warm-wheel reduction mechanism.
Mechanism of climbing robot using its own weight
It is desirable that a climbing robot has more than two wheels, since it is quite possible for a wheel to slip out of place; more wheels will contribute to stable climbing. As shown in Figure 1, our climbing robot is equipped with four active wheels. Two wheels are located on top (numbers 1 and 2) and two wheels are located on the bottom (numbers 3 and 4). Each wheel is placed at the same angle ± π / 4 rad relative to the x-axis when viewed from the top of the cylinder.
The active wheel is driven by a DC servomotor via a warm-wheel reduction mechanism. The warm-wheel reduction mechanism, which has non-back drivability, allows the robot to be at rest without any energy expenditure when the input electric current for the servomotor is zero.
We ensured that the center of mass of the robot is located outside of the cylinder by placing the control system at the side of the down-side active wheels. Each of the four active wheels has a steering system to control the steering angle. The steering system is driven by a DC servomotor via a warm-wheel reduction mechanism.